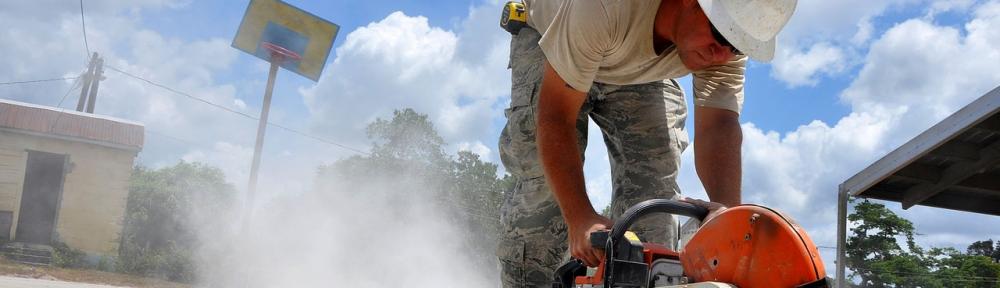
Don’t let your health and safety measures gather dust
Posted on July 3, 2023
We were recently approached by a company for advice on its health and safety measures after being told by the Health & Safety Executive (HSE) that there was room for improvement in its approach.
It’s the kind of work we routinely undertake given our expertise.
During their visit, HSE inspectors saw too much evidence of dust. This particular company’s operations is woodworking machines meaning the creation of respirable dust and, dust as we have previously discussed can be a significant hazard, especially for maintaining good lung function. This company’s machines have local exhaust ventilation (LEV) attachments which clearly had not been effective enough to prevent accumulation and a subsequent HSE warning.
We have now advised our client to check for blocks in the LEVs’ ductwork, to bring in a specialist engineer to test the machines and to make sure periodic testing now happens to ensure that the LEVs remain as effective as possible. The ultimate response, of course, is to buy new machines which is exactly what our client is also doing, as well as redesigning their extraction system. It may have taken an HSE inspection to set those wheels in motion, but they are doing the right thing, protecting their employees over the long term and making sure appropriate control measures are in place. Not to do so is putting the business in a hazardous place!
Understand the hazards
This client are good manufacturers, they are good at their job, but that is not enough to be regarded as a competent employer, what matters is understanding the hazards being created as a result of the work. That’s competency and respect. Courtley’s role is to help our clients keep on top of these matters, to help our clients do the right thing. Every time. So as part of our advisory role we have been checking all other potential hazards, for example how adhesives and solvents are stored and what their manual handling regime looks like.
This helps guard against complacency. Just “part of the job” practices don’t cut it as a defence in the face of prosecution or financial penalties. While I love going into companies and onto sites and praising what I see – “You are doing well, just a few little tweaks and you’re there” – I get an equal amount of satisfaction to say: “You are not as good as you think you are, other similar companies would be approaching it in a much more controlled way.”
COSHH courses
Our Control of Substances Hazardous to Health (COSHH) training is about understanding the processes from start to finish. COSHH is a law which puts companies under an obligation to control substances which could pose a danger to employees or members of the public. It should be regarded as a priority because chemical (and dust) incidents can have a detrimental effect on employees, other workers and members of the public. Any substance deemed hazardous to health must be assessed for potential risks, so procedures can be implemented to reduce or remove them. COSHH assessments play an important role in reducing these risks.
We assist companies by regularly conducting information searches on substances and keeping up to date with any new information or guidelines; developing the safe working practices within a business’s operations to limit or remove the risks associated with the substances used; establishing a robust system of recording and document control for a safety file; providing ongoing monitoring of hazardous substances.
Dust is created by a process – cutting, grinding etc, so COSHH is not just for hazardous substances brought into a place of work. The timber brought in a woodcutting workshop is not a problem in itself, but when the blades come out, that’s when it can become a problem.
Control measures
It’s the kind of discussion we have with clients to look at it from their own ‘global’ perspective, to think of the COSHH regulations and how they apply to them and that comes down to robust application of the hierarchy of control measures. In that process, you have to be careful that your measures to protect against risk aren’t creating another risk possibly greater than the one under scrutiny. I often say that my nightmare is someone’s safety helmet falling off and hitting someone else on the head!
Control measures are about people understanding what they are there for and getting that ‘buy in’.
That’s culture, that’s embedding the right behaviours. And that is health and safety.